PA 66 Flame Retardant Grade
Introduction
This product is a composite of PA 66 and flame retardant. Flammability class is UL94 V0 (1 / 8”, 1 / 16”, 1 / 32”, 1 / 64’’ thickness of specimens). Such product has advantages of toughness, moldable property, heat stability, dimensional stability and non-corrodibility. Therefore, it is suitable for using on precise electronic injection parts featured with its light, short and small properties.
Applications
1. Connectors
2. Bobbin
3. Transformer
2. Bobbin
3. Transformer
Features
1. Excellent case hardness, low friction factor, wear-resistance and excellent self-lubrication.
2. Excellent fire retardancy
3. Excellent chemical resistance
3. Excellent gas-barrier property
5. Easy processability
2. Excellent fire retardancy
3. Excellent chemical resistance
3. Excellent gas-barrier property
5. Easy processability
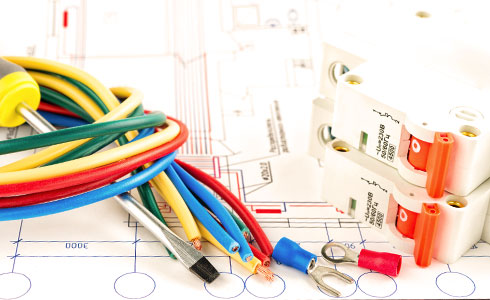
Mechanical properties | Standard | Unit | Test sample conditions | PA 66 Flame Retardant Grade | |
---|---|---|---|---|---|
I11(X) | |||||
Tensile Strength at Yield | ASTM D638 | Kg/cm2 | Dry / Cond* | 850 / 550 | |
Elongation at Break | ASTM D638 | % | Dry / Cond* | 10 / 30 | |
Tensile Strength at Break | ASTM D638 | Kg/cm2 | Dry / Cond* | 800 / 500 | |
Tensile modulus | ASTM D638 | Kg/cm2 | Dry / Cond* | 35000 / 22000 | |
Flexural strength | ASTM D790 | Kg/cm2 | Dry / Cond* | 1200 / 750 | |
Flexural modulus | ASTM D790 | Kg/cm2 | Dry / Cond* | 30000 / 18000 | |
Izod notched impact strength | ASTM D256 | Kg-cm/cm | Dry / Cond* | 3.0 / 4.5 | |
Thermal-fr properties | |||||
Melting temperature | ASTM E967-DSC | °C | - | 260 | |
Heat deflection temperature, 4.6 ㎏/cm2 (66 psi) | ASTM D648 | °C | - | 235 | |
Heat deflection temperature, 18.5 ㎏/cm2 (264 psi) | ASTM D648 | °C | - | 85 | |
Flammability | UL94 | - | - | V0 | |
Physical properties | |||||
Hardness | ASTM D2240 Shore D | D | Dry / Cond* | 80 / 78 | |
Density | ASTM D792 | g/cm3 | - | 1.17 | |
Molding shrinkage normal or perpendicular | ASTM D955 | % | - | 1.0 |
Test sample conditions, Test sample conditions, Dry= Measurements at 23°C, RH50. Test after molded 1 - 2 hr. Cond*=Test according to ISO 1110 conditions. For reference only.
PA 66 / PA 6 Flame Retardant with Glass-fiber Reinforced Grade
Introduction
This product is a composite of PA 66, PA 6, flame retardant and 30 % glass-fiber for reinforcement. Flammability class is UL94 V0 (1/8”, 1/16”, 1/32” thickness of specimens). It is no efflorescence grade. Such product has excellent flame resistance, strength and electric properties, also has good moldable property, heat stability and non-corrodibility.
Applications
1. Cable connector
2. Switch, socket
3. Electric components
2. Switch, socket
3. Electric components
Features
1. Good stiffness
2. Excellent fire retardancy
3. Higher heat deformation temperature
2. Excellent fire retardancy
3. Higher heat deformation temperature
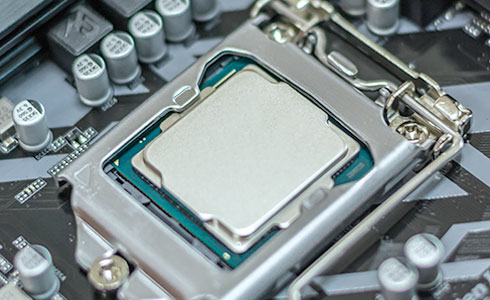
Mechanical properties | Standard | Unit | Test sample conditions | PA 66 / PA 6 Flame Retardant with Glass-fiber Reinforced Grade | ||
---|---|---|---|---|---|---|
G-4130-I1043-(#) | G-4130-I1046-(#) | G-4130-I1047-(#) | ||||
Tensile Strength at Yield | ASTM D638 | Kg/cm2 | Dry / Cond* | 1350 / 1050 | 1689 / 1400 | 1750 / 1450 |
Elongation at Break | ASTM D638 | % | Dry / Cond* | 3.5 / 5 | 2.5 / 4 | 2 / 2.5 |
Tensile Strength at Break | ASTM D638 | Kg/cm2 | Dry / Cond* | 840 / 800 | 1120 / 1030 | 1480 / 1050 |
Tensile modulus | ASTM D638 | Kg/cm2 | Dry / Cond* | 52200 / 41200 | 63300 / 52000 | 65000 / 55000 |
Flexural strength | ASTM D790 | Kg/cm2 | Dry / Cond* | 2100 / 1750 | 2330 / 1740 | 2400 / 1870 |
Flexural modulus | ASTM D790 | Kg/cm2 | Dry / Cond* | 69500 / 47500 | 101400 / 64200 | 111700 / 75400 |
Izod notched impact strength | ASTM D256 | Kg-cm/cm | Dry / Cond* | 9.0 / 11.5 | 11 / 13.0 | 10.0 / 11.5 |
Thermal-fr properties | ||||||
Melting temperature | ASTM E967-DSC | °C | - | 260 | 260 | 260 |
Heat deflection temperature, 4.6 ㎏/cm2 (66 psi) | ASTM D648 | °C | - | - | - | - |
Heat deflection temperature, 18.5 ㎏/cm2 (264 psi) | ASTM D648 | °C | - | 240 | 240 | 240 |
Flammability | UL94 | - | - | V0 | V0 | V0 |
Physical properties | ||||||
Hardness | ASTM D2240 Shore D | D | Dry / Cond* | 79 / 79 | 80.5 / 79.5 | 81 / 81 |
Density | ASTM D792 | g/cm3 | - | 1.49 | 1.65 | 1.73 |
Molding shrinkage normal or perpendicular | ASTM D955 | % | - | 0.46 | 0.34 |
Test sample conditions, Test sample conditions, Dry= Measurements at 23°C, RH50. Test after molded 1 - 2 hr. Cond*=Test according to ISO 1110 conditions. For reference only.
PA 66 / PA 6 with Heat-stabilized / Thermal Resistance Grade.
Introduction
Grades:
1. Hot-oil resistance, for injection molding, glass-fiber reinforced PA 66 or PA 6.
2. Long term thermal resistance, for injection molding, glass-fiber reinforced PA 66 or PA 6.
Applications:
This product has been commonly used in production for equipment against erosion of hot oils, machinery component with high stiffness and dimensional stability requiring contact with hot oils and housings, for example: coil cage, bearing cage, electrical insulating products. Its long term thermal property is suitable for equipment requiring high stability against decrease of mechanical properties under high-temperature condition, such as inject pipe of automotive inlet manifold etc.
Notes:
All raw materials are under strict inspection and monitor during preparation processes, the materials are all RoHS certified.
1. Hot-oil resistance, for injection molding, glass-fiber reinforced PA 66 or PA 6.
2. Long term thermal resistance, for injection molding, glass-fiber reinforced PA 66 or PA 6.
Applications:
This product has been commonly used in production for equipment against erosion of hot oils, machinery component with high stiffness and dimensional stability requiring contact with hot oils and housings, for example: coil cage, bearing cage, electrical insulating products. Its long term thermal property is suitable for equipment requiring high stability against decrease of mechanical properties under high-temperature condition, such as inject pipe of automotive inlet manifold etc.
Notes:
All raw materials are under strict inspection and monitor during preparation processes, the materials are all RoHS certified.
Features
Due to the addition of special heat-stabilizer, comparing with normal glass-fiber reinforced PA 66 composite, this product has following properties:
● It has better mechanical performance, flowability and can be easily processed to complex parts.
● With its hot-oil resistance property, it forms a protection against brittleness and early decrease of the mechanical properties and a protection against the erosion of hot oil, glycol, fats etc.
Compared with common glass-fiber reinforced PA 66, this product performs better functions after undergoing 1,500hr – 5,000hr at high-temperature condition. Therefore, its long term thermal stability property is suitable for manufacturing automotive components, such as air intake manifold…
● It has better mechanical performance, flowability and can be easily processed to complex parts.
● With its hot-oil resistance property, it forms a protection against brittleness and early decrease of the mechanical properties and a protection against the erosion of hot oil, glycol, fats etc.
Compared with common glass-fiber reinforced PA 66, this product performs better functions after undergoing 1,500hr – 5,000hr at high-temperature condition. Therefore, its long term thermal stability property is suitable for manufacturing automotive components, such as air intake manifold…
Processing guidelines
Drying condition:
To avoid degradation during injection, drying is required prior to injection molding. Drying temperature: 95-100 ℃, drying time: 3-4 hours.
Recommended injection conditions:
Injection temperature: 270-285 ℃
Injection pressure: 80-120 MPa
Mold temperature: 60-80 ℃
To avoid degradation during injection, drying is required prior to injection molding. Drying temperature: 95-100 ℃, drying time: 3-4 hours.
Recommended injection conditions:
Injection temperature: 270-285 ℃
Injection pressure: 80-120 MPa
Mold temperature: 60-80 ℃
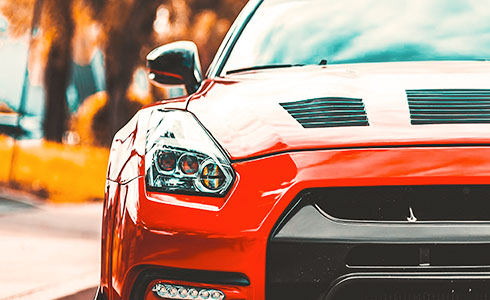
Mechanical properties | Standard | Unit | Test sample conditions | PA 66 with Heat-stabilized / Thermal Resistance Grade |
PA 6 with Heat-stabilized / Thermal Resistance Grade |
---|---|---|---|---|---|
G-1125-H | G-4033-H | ||||
Tensile Strength at Yield | ASTM D638 | Kg/cm2 | Dry / Cond* | 1450 / 1100 | 1670 / 1370 |
Elongation at Break | ASTM D638 | % | Dry / Cond* | 5 / 7 | 5 / 8 |
Tensile Strength at Break | ASTM D638 | Kg/cm2 | Dry / Cond* | 1450 / 1100 | 1670 / 1370 |
Tensile modulus | ASTM D638 | Kg/cm2 | Dry / Cond* | 48600 / 36100 | 59400 / 37000 |
Flexural strength | ASTM D790 | Kg/cm2 | Dry / Cond* | 2400 / 1900 | 2700 / 2030 |
Flexural modulus | ASTM D790 | Kg/cm2 | Dry / Cond* | 58500 / 29900 | 79700 / 37100 |
Izod notched impact strength | ASTM D256 | Kg-cm/cm | Dry / Cond* | 7 / 9 | 12.5 / 15 |
Thermal-fr properties | |||||
Melting temperature | ASTM E967-DSC | - | Dry / Cond* | 260 | 220 |
Heat deflection temperature, 4.6 ㎏/cm2 (66 psi) | ASTM E967-DSC | - | - | - | - |
Heat deflection temperature, 18.5 ㎏/cm2 (264 psi) | ASTM E967-DSC | - | - | 235 | 200 |
Flammability | UL94 | - | - | HB | HB |
Physical properties | |||||
Hardness | ASTM D2240 Shore D | D | Dry / Cond* | 83 / 81 | 83 / 82 |
Density | ASTM D792 | Kg/cm2 | - | 1.32 | 1.38 |
Molding shrinkage normal or perpendicular | ASTM D955 | % | - | 1.39 | 0.99 |
Test sample conditions, Test sample conditions, Dry= Measurements at 23°C, RH50. Test after molded 1 - 2 hr. Cond*=Test according to ISO 1110 conditions. For reference only.